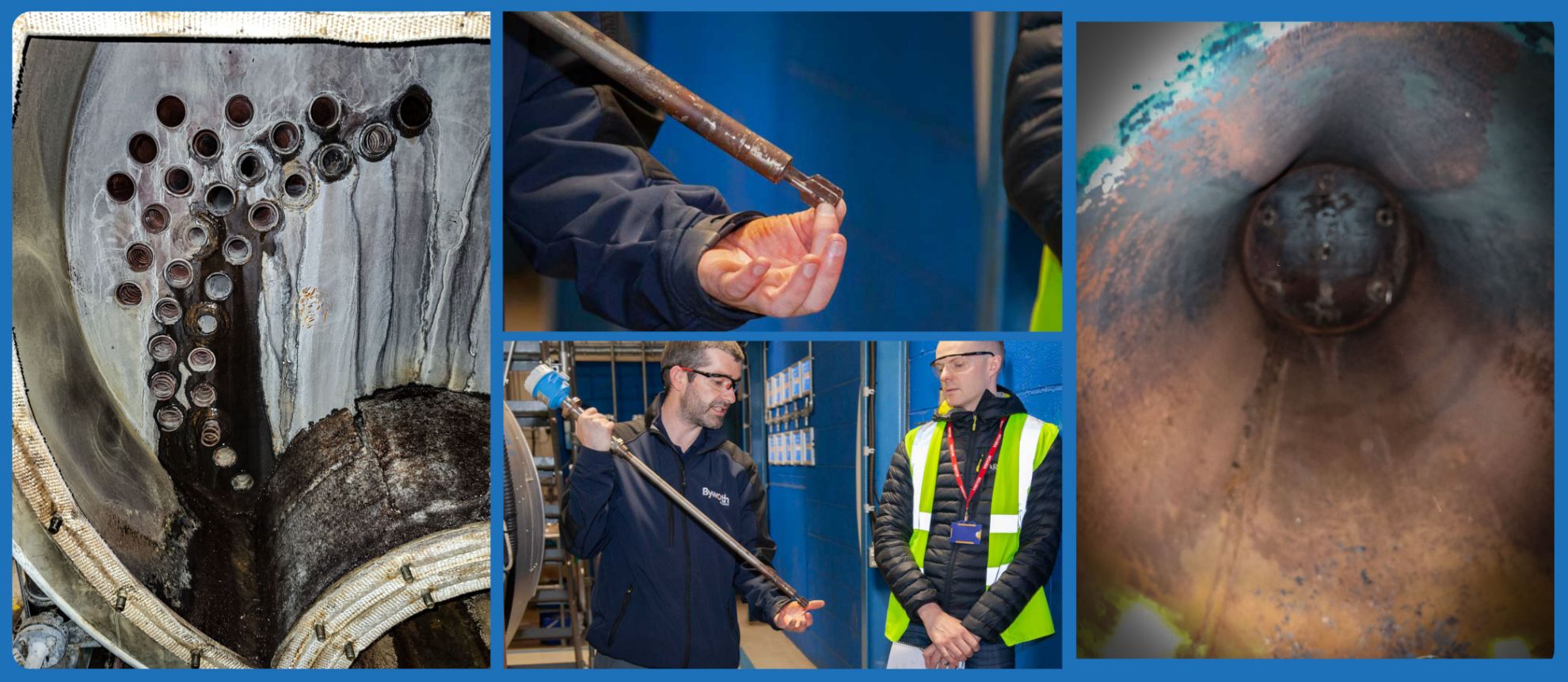
Posted 30th August 2024
Dangerous low water in industrial boilers
Industrial boilers are critical components in many manufacturing processes, providing the steam necessary for various applications. However, one of the most significant threats to the safe and efficient operation of a boiler is dangerous low water. This blog explores the causes, dangers, identification, and prevention of dangerous low water in industrial boilers, as well as the advanced technologies available to mitigate these risks.
What is Dangerous low water
Dangerous low water is the term used to describe a low water condition when the burner is still firing. There are many safety features that should shut down a burner when a boiler reaches low water, however factors such as scale and foam can prevent these working effectively, and result in dangerous low water.
What Causes Low Water Conditions?
There are several factors that can contribute to low water levels in your boiler such as –
-
Contamination and poor water quality – Poor quality water can significantly impact the accuracy of water level reading.
-
Human error – Poor monitoring or maintenance, likely due to lack of training.
-
Improper Blowdown Procedures - Excessive blowdown can inadvertently lower water levels if not carefully managed.
-
Feedwater pump failure - This is a common culprit, as the pump is responsible for supplying water to the boiler.
-
Control valve malfunction - Faulty valves can disrupt the water flow to the boiler resulting in inadequate water levels.
-
Sudden increase or change in steam demand - A rapid rise in steam load can temporarily reduce water levels until the feedwater system can compensate.
-
Leakage - Undetected leaks in the boiler or associated piping systems can cause water levels to fall below safe operating levels.
Boilers are designed and built to cope with most situations regarding low water conditions. An issue presents when the burner continues to fire during these conditions.
What are The Dangers of Low Water?
The consequences of low water conditions are severe and can be highly dangerous.
-
Reduced boiler efficiency - Low water levels can impact boiler efficiency and performance.Reduced boiler efficiency - Low water levels can impact boiler efficiency and performance.
-
Overheating and metal failure - When water levels drop below safe limits, boiler tubes and other metal components are exposed to extreme heat. When this heat intensity reaches its peak, parts begin to fail, leading to costly repairs and downtime.
-
Catastrophic failure of pressure vessel - In extreme cases, dangerous low water can cause boiler explosion, putting lives and property at risk.
Identifying and Preventing Low Water Conditions
Early prevention and identification of low water conditions are crucial to maintaining safe and efficient boiler operations. The best strategies for preventing low water include a combination of the following.
-
Flue Temperature – An increase in flue temperature is the first key indicator that something is wrong with the pressure vessel.
-
Testing – Weekly* water level testing by evaporation and water quality testing which must be logged.
-
Regular Monitoring - Routine checks of water levels using gauge glasses, or electronic level indicators, as well as daily* checks of the flue temperature.
-
Operator Training - Comprehensive training programs for boiler operators to recognise signs of low water conditions and take corrective actions promptly.
-
Maintenance - Regular maintenance of feedwater systems, pumps, and control valves to ensure they are functioning correctly.
-
Automation and Control Systems - Implementing automated control systems that can detect and correct water level issues without human intervention. However, these should not be solely relied upon as contamination such as scale will compromise all level detection equipment.
*The frequency of your checks are dictated by your boiler arrangement and the type of equipment on site.
Advanced Technologies for Water Level Monitoring
Several advanced technologies can provide accurate and reliable water level monitoring for your industrial boiler including:
-
Vibrating fork level
sensors - These devices use the principle of vibration frequency change to
detect the presence or absence of water at a specific level. When the water
level drops below the fork, the frequency changes, triggering an alarm or
control action.
-
Guided Wave Radar (GWR) - GWR technology involves sending microwave pulses down a probe and measuring the time it takes for the pulses to reflect back from the water surface. This provides precise and reliable water level measurements, even in harsh conditions.
-
Conductivity Probes - Conductivity probes detect water levels based on the electrical conductivity of water. When water levels drop below the probe, the electrical circuit is broken, triggering an alarm or control response.
-
Ultrasonic Level Sensors - These sensors use ultrasonic waves to measure water levels. They are non-intrusive and can provide accurate measurements in a variety of boiler conditions.
Although all these methods are considered effective in identifying low water conditions, we advise investing in more than one method for added safety and peace of mind.
The best line of defence to protect your boiler is to ensure operators are correctly trained to maintain a healthy plant. By understanding the causes, dangers, and prevention methods for low water conditions, operators can significantly reduce the risk of boiler-related incidents and ensure the safe and efficient operation of your boiler and boiler house equipment.
What is the best fuel to power industrial boilers?
Which is the best, most cost effective fuel for your operations? Find out in our blog all about fuel options.