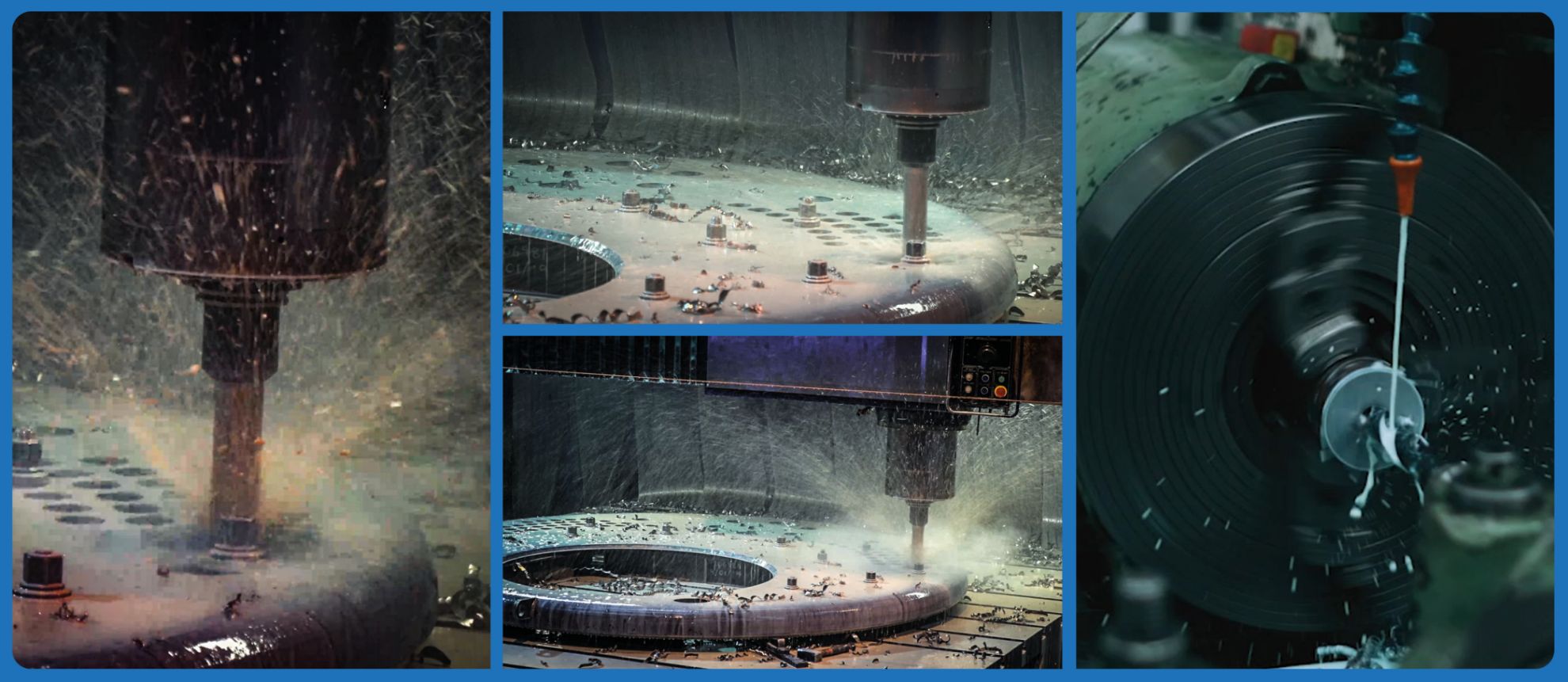
Safety Procedures in the workplace
Volume 3 – Metalworking Fluid Risks
Posted 26th January 2024
Metalworking fluid is the term used for the substance used during the machining of metals to lubricate and cool the materials. It is also used to carry away debris and fine metal particles, which can be dangerous for operators. MWF can improve machining performance and is also important for prolonging the life of machinery by providing corrosion protection and lubrication.
MWF is used throughout our manufacturing facility including all band saws, CNC milling machines and lathes. The fluid stays within the machine and deteriorates over time, developing harmful bacteria and presenting hazards to the machine operator and potential issues with the machine. The effective maintenance of the fluid is key to controlling the risks and creating a safe working environment when using MWF.
What are the risks from working with metalworking fluids?
Metalworking fluids can pose health risks through three main routes:
- Inhalation: Mists generated during machining can carry harmful bacteria, mineral oils, and chemicals, leading to respiratory problems like occupational asthma and lung infections.
- Ingestion: Accidental swallowing of contaminated fluids can cause skin and stomach irritation.
- Skin contact: Direct contact with fluids can lead to dermatitis, allergic reactions, and even chronic skin conditions.
But it’s not all doom and gloom, the good news is that these risks can be effectively prevented or minimised with correct and efficient safety measures
What actions do we take when using Metalworking Fluid?
The Control of Substances Hazardous to Health (COSHH) regulations requires employers to identify, assess, and control risks from hazardous substances, including metalworking fluids. This means carrying out risk assessments, implementing control measures, providing training, and monitoring exposure levels.
Our health and safety expert Jon carries out the following tasks to ensure equipment and fluid are safe:
- Weekly checks on all Metalworking Fluids around Byworth Boilers manufacturing facility.
- Once a month a Dip slide sample is taken to check levels of bacterial contamination, Regular checks, and actions to maintain the fluid quality.
- PH readings once a week to check for corrosion, if the PH reading is low, adjustments are made to the concentration of the coolant mix, MP Millersol (Normally 7.2 to 9.0).
- Monthly Band Saws are cleaned out with fresh metal working fluid by a competent person, wearing chemical gloves, eye protection, stealth respirator, safety boots, ear protection.
- Once a Year Asquith Butler CnC Machine is cleaned out by Millers Oil, replaced with new COSHH MP Millersol
- A risk assessment is in place for Working Band Saws, Lathe Machines, Asquith Butler CnC machine MP Millersol Coolant.
- All Coolant waste is transported of site by Waste Contractor, Oil recoveries /Millers Oil.
Looking after our team
In addition to the above procedures it is also essential that our operators are correctly trained and educated on how to safely work with these substances, and that safety precautions are in place to minimise risks. We:
- Provide full training and frequent recap sessions on the dangers or working with metalworking fluids.
- Provide full personal protective equipment (PPE) for all operators including chemical gloves, eye protection, stealth respirator, and safety boots.
Our fully trained Health and Safety officer Jon Wilkinson is responsible for ensuring every team member is fully aware of the risks and procedures in place for working with MWF and conducts regular refresher training in all areas of health and safety to help protect our workforce.
Follow us on social media for all the latest news and updates from the Byworth team
Not sure which boiler is right for you?
Call us on +44 (0)1535 665225 and we will advise you on the best product for your needs.