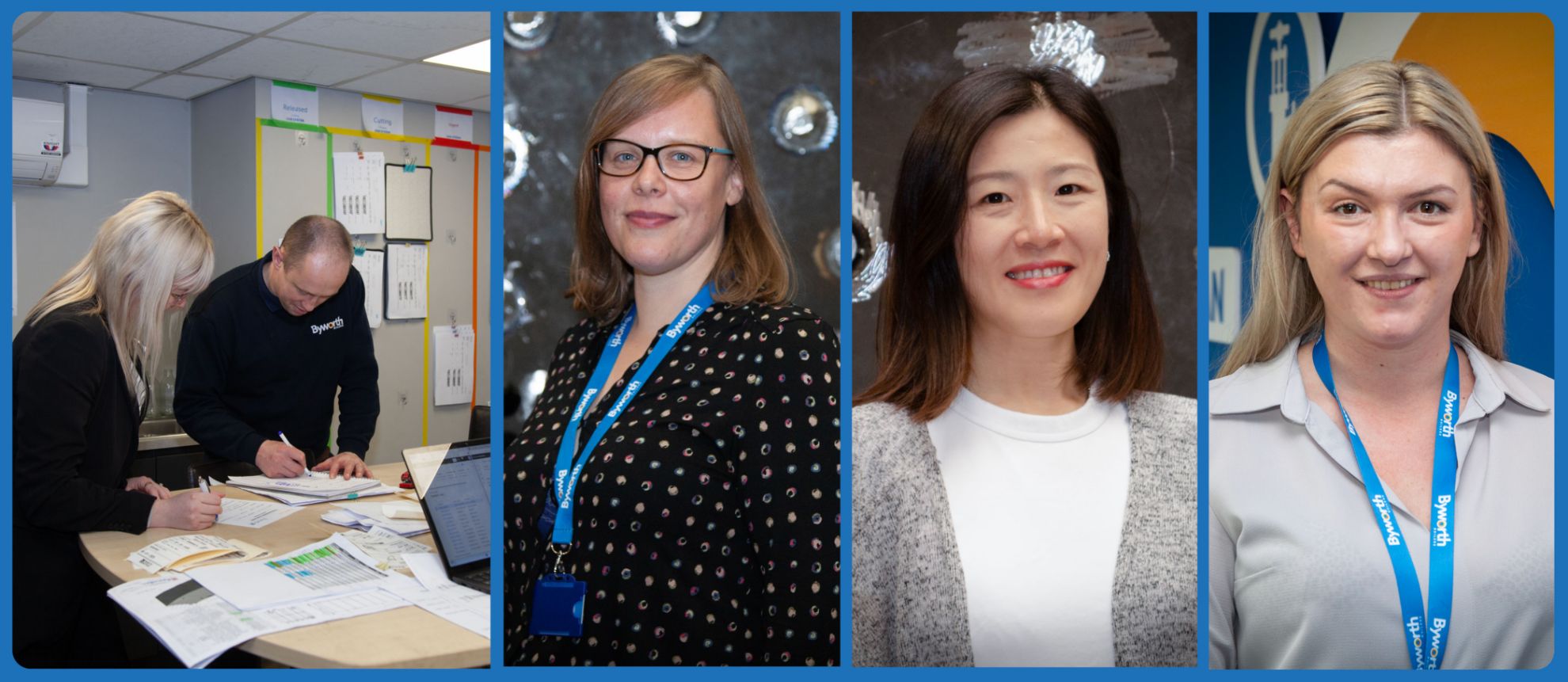
A New Era of Efficiency
Posted February 24th 2025
How Byworth Boilers is Streamlining Operations
At Byworth we have always been committed to innovation and operational excellence, but as the needs of the industry changes we must continue to focus our attention on improving manufacturing processes and products for the future. Continuous improvement is essential if we are to remain competitive and maximise potential. A key aspect of the improvements we have made has been the creation of new roles within the organisation aimed at enhancing efficiency, driving technological advancements, and meeting the evolving needs of the market.
In 2024, three new employees joined Byworth Boilers, bringing with them fresh perspectives and specialised expertise. These positions were designed to support the company’s strategic goals, streamline operations, and ultimately improving the customer experience.
We had a quick Q&A session with the three individuals to explore the contributions they’ve made and how their expertise is driving positive change within Byworth Boilers.
Alisha Bell - ERP Analyst
1. Tell us about your role at Byworth and what it involves?
My role is ERP Analyst which entails working closely with design, projects and manufacture to improve workflows within ERP and internal processes.
My day-to-day activities include writing manufacturing routes for all products, reviewing technical drawings, ensuring data within the system has been inputted correctly, and implementing structure through documentation with process control change requests and lessons learnt.
2. How do you feel this role has impacted the workflow at Byworth?
My role has minimised errors within production and allowed for more thorough lead times for our customers. Going forward this will have a significant impact on our ability to meet and exceed customer expectations.
Additionally, I analyse concerns and then implement and manage systems that align accordingly. We can then make changes to improve customer satisfaction and our manufacturing capabilities.
3. What challenges have you faced that stand out? Were you able to overcome them or are they on going?
One of the key challenges for me was analysing the data from the previous system. It’s lack of consistency had a significant impact on the business internally and externally and correcting this for the new set up was challenging.
I have overcome these challenges by rewriting the manufacturing routes and conducting a detailed analysis of parts that are set up. This ensures information is correct for both current and future projects.
4. What changes have you implemented that have had a positive impact on the business?
I have introduced workflows (PDCR and lessons learnt) which are used across the business, allowing clear communication on issues impacting the company.
Additionally, all drawings, routes and BOMs (bill of materials) are now activated by myself. This ensures a tight level of control minimising the possibility of errors within manufacture, and prevents delays on the supply of products.
5. How has your past working experiences helped you in this current role?
I previously ran a similar system which highlighted the importances of processes and procedures needed within a business in order to run efficiently.
My background in both manufacture and design allows me to make decisions in consideration of the impacts on various areas and what will benefit the teams in the long run.
Shir Lee Ong – Planning Coordinator
1. Tell us about your role at Byworth and what it involves?
In my role as Planning coordinator, I schedule and plan the manufacturing works according to the required delivery dates.
I work closely with our Supply Chain Team to ensure material availability and production deliveries coordinate with the agreed delivery date.
My role also involves -
· Checking BOM, route and drawing availability before releasing WOs.
· Gatekeep on the accurate information flow.
· Improving the current process and creating reports to help with delivery.
Due to my previous experience with the system, every so often, I am IT helpdesk for the team on Microsoft Dynamics issues.
2. How do you feel this role has impacted the workflow at Byworth?
Help the team to prioritise works better, work with more efficiency and accurate information flows. Try to convince and get people to understand the system better
-
What
challenges have you faced that stand out? Were you able to overcome them
or are they on going?
Mainly helping to change the mindset of people and getting them on board with a more positive mental attitude towards the processes. Changes don’t happen overnight and improvements do not happen straight away which can lead to frustrations and negativity towards a new way of working.
It has been challenging learning the system and products as I go but I am surrounded by a supportive and knowledgeable team which is great.
-
What
changes have you implemented that have had a positive impact on the
business?
Scheduling and plan work going into manufacturing as well as making sure all the information required beforehand is available. This has helped the flow of manufacturing.
Maximise the system through better understanding of the structure and how it works.
-
How has your past working experiences helped you in this current role?
The years of manufacturing experience has helped me to understand the needs of the business and how to tackle some of the on-going issue such as production planning, ERP and continuous improvements.
Kirsty Pilbin – Project Manager
1. What is your role at Byworth boilers and what does this role involve?
It is the Project Team’s responsibility to look after projects from initial handover from the Sales team, through design, production and commissioning and into Warranty claims. As Project Manager I oversee all projects ensuring a consistent level of communication for both customers and internal teams.
2. How do you feel this role has impacted the workflow at Byworth?
My role is to improve the flow of information between departments, and to the customer. We are continually striving for better communication of relevant information between departments.
3. What changes have you implemented that have had a positive impact on the business?
One of the first activities implemented was the “Sunrise” meeting. A quick daily meeting to review open actions across departments. The meeting aims to improve product flow through production by highlighting activities that have not been completed which could affect the build rate, and addressing them before they become an issue. Addressing issues and troubleshooting with relevant departments on a daily basis has had a significant impact on our workflow and improved communication and operational efficiency across manufacturing.
4. How has your past working experiences helped you in this current role?
I worked for an access platform manufacturer for 11 years in various roles in the Design, Cost and Project departments. This gave me key insights into lean manufacturing principles and pre-production development which have been useful in my role here.
The future is bright
These insights shared by Alisha, Shir Lee, and Kirsty highlight the positive impact their new positions have had on streamlining operations, improving communication, and ultimately, enhancing the customer experience.
From optimising ERP workflows and ensuring data integrity, to coordinating manufacturing schedules and fostering positive attitudes towards process changes, to overseeing projects and proactively addressing potential roadblocks, the team are driving efficiency and fostering a culture of proactive problem-solving.
We hope this demonstrates our commitment to continuous improvement and the future of the Byworth brand.