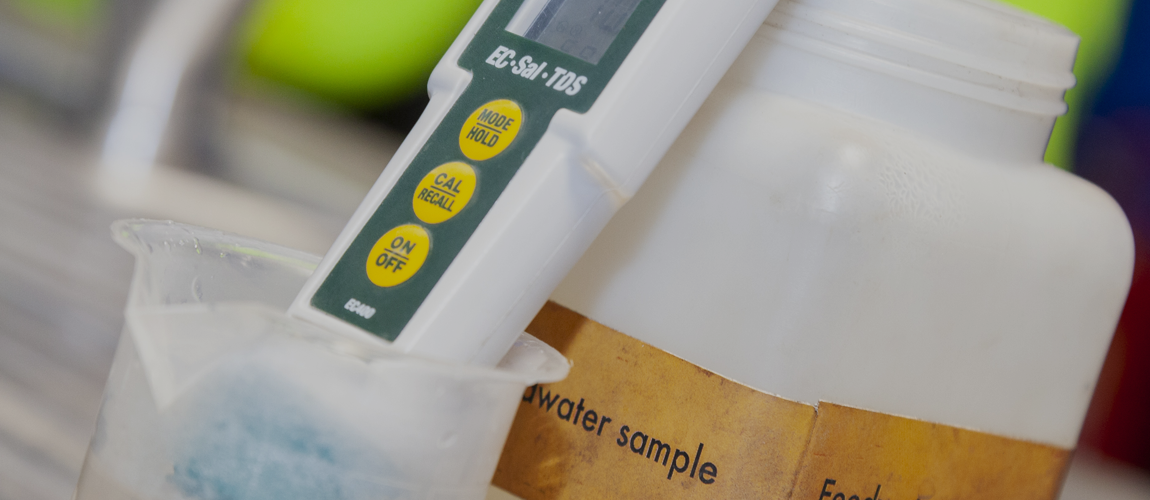
The importance of water treatment for your industrial boiler
Why do you need water treatment training?
It is your responsibility to take ownership of your water quality and water treatment processes.
The water quality in your boiler has a big impact on energy efficiency and the reliability of your whole steam system. It will play a huge role in the life expectancy of your industrial boiler.
Things can easily go wrong when you don’t test, record, and manage your water quality efficiently. For every 1000kg/hr of steam exported, boilers consume approximately 1 tonne of water, leaving any contamination behind inside the vessel, these images show an example of the consequences of poor water treatment.
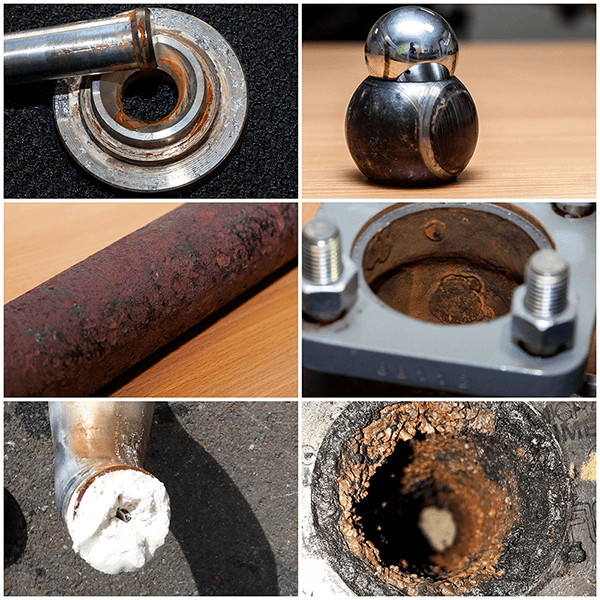
Poor or inadequate steam boiler water treatment has been shown to be the cause of a large proportion of boiler failures. The common reasons include:
- Non-operation of controls due to sludge accumulation
- Perforation of smoke tubes due to corrosion
- Most serious of all - overheating, distortion and collapse of the furnace caused by scale and other deposits, which can lead to dangerous low water.
- (Read more about dangerous low water here)
All this can be avoided by implementing correct boiler water treatment.
Testing your water quality is a key part of boiler operation and maintaining your testing and water quality in line with your water treatment risk assessment should be one of the core duties of your boiler operators.
The following best practice water treatment tips will help you keep your boiler working safely and efficiently.
Filtration
Where water has been taken from a source other than a potable one, you may need to filter the water to remove solid matter. A number of techniques can be used depending on the source:
- Sedimentation (allowing time for heavier particles to sink naturally)
- Clarification (using charged particles to attract fine suspended solids into clumps that subsequently sink)
- Sand/carbon filtration
Water Softening
When it comes to industrial boilers all mains water is hard water even if you are located in an area considered to have soft water. The amount of hardness salts must be lowered below two parts per million (measured as calcium carbonate) for optimum efficiency. If this level is not maintained, a hard ‘rock-like’ substance (scale) forms on the heat transfer surfaces of the boiler forming an insulating layer. This will vastly reduce your boilers efficiency and have a significant impact on the metal temperatures.
It is also possible for the solid material to break off and collect in the bottom of the boiler. Left unchecked, insulated surfaces can overheat and crack leading to leaks or even catastrophic failure.
To avoid this, we recommend one of the following water softening techniques.
Base exchange softening.
The simplest and probably most commonly used method. A resin bed is ‘charged’ with sodium ions by washing it with a strong brine solution. As hard water passes over the resin, the sodium is substituted for the calcium or magnesium ion in the water. The resultant sodium compounds will not deposit out in the boiler, therefore preventing scale formation. These dissolved solids are instead removed by TDS blowdown. Once the resin bed has been exhausted, it is again recharged using a brine wash.
De-alkalisation
De-alkalisation differs from base exchange by exchanging ions of calcium and magnesium for hydrogen instead of sodium, thus converting alkaline hardness elements to water and carbon dioxide (also reducing the level of dissolved solids). The carbon dioxide is then extracted through a de-gassing tower. The now acidic water is then treated to raise the pH above 8.5 before being passed, if necessary, to a base exchange softener to remove any non-alkaline hardness.
De-mineralisation
De-mineralisation units produce water with very low levels of dissolved solids by removing all minerals. The units work by first passing the water through a strong acid to remove the cations and then a base solution to remove the anions. Reverse Osmosis (RO)
De-aeration
To remove dissolved oxygen and carbon dioxide through mechanical means.
Control total dissolved solids (TDS)
As water is boiled within the boiler and steam is produced, solids remain in the water and concentrate. Thus, over time the level of total dissolved solids (TDS) increases. Controlling the TDS is achieved by either continuous or intermittent blow down.
Control deposition
Any deposits in the boiler can only come from the feed water. Control of the deposits is of high importance to maintain the efficiency of the heat exchange surfaces within the boiler. The two main methods of deposition control are by either carbonate or phosphate control.
These are just a few pointers to keep in mind when operating and managing an industrial boiler.
If you'd like to know more about correct boiler water treatment, contact our Training Team who will be more than happy to explain the water treatment training on offer at Byworth.
Our City and Guilds assured training course is one of the best ways to learn the ins and outs of water treatment. Read our blog on the course and explore it's advantages via the link below.
Not sure which boiler is right for you?
Call us on +44 (0)1535 665225 and we will advise you on the best product for your needs.